¿Cómo ordenar y diseñar circuitos impresos en formato panel para ensamble?
Por: Microensamble.com, abril 28 de 2016
Panelización es el proceso de agrupar circuitos impresos de una o diferentes referencias, con el objeto de facilitar los diferentes procesos de fabricación y ensamble de tarjetas electrónicas.
Independientemente de si el proceso de ensamble de las tarjetas va ser manual o automatizado, las siguientes razones deben ser consideradas para agrupar varios circuitos en un panel:
- Cantidad de tarjetas: Los procesos de inserción de componentes convencionales y ensamble manual o automatizado de componentes SMD, son mucho más eficientes ya que permiten colocar el mismo componente a un número de tarjetas agrupadas en panel y no a una sola al tiempo. En el caso de usar maquinas Pick & Place, se colocarán automáticamente sobre la pasta de soldar, todos los componentes de montaje superficial (SMD), quedando disponible el panel para su proceso de soldadura o inspección de defectos.
- Bordes de sujeción: Permite colocar bordes de panel para el manejo y/o transporte en los procesos de ensamble, soldadura e inspección. En ocasiones por requerimientos de diseño, nuestros circuitos son muy pequeños o tienen forma circular o irregular o no poseen bordes libres de componentes, presentando dificultades para su manejo al ser colocados en cualquier dispositivo de sujeción manual o automático. Dichos bordes podrán contener ayudas para el ensamblador, tales como marcas de dirección de desplazamiento por el proceso de soldadura automatizado, perforaciones de sujeción y/o fiduciales (marcas de referencia) para el posicionamiento exacto de las maquinas que intervienen en los diferentes procesos automatizados, referencia, serialización, etc..
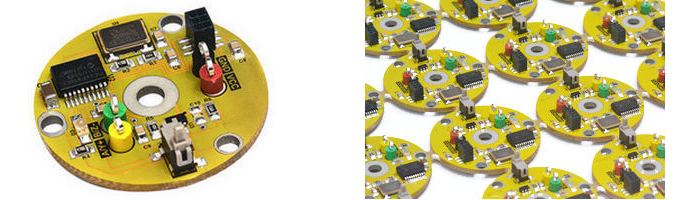
- Aplicación de la soldadura en pasta: Es uno de los procesos donde se obtiene gran eficiencia. Normalmente utilizamos jeringas para dispensar manual o automáticamente, soldadura o adhesivo a una tarjeta. Agrupar circuitos en panel permite el uso de un stencil para efectuar el mismo proceso a un grupo de tarjetas en un solo paso en lugar de hacerlo dispensando punto a punto a un solo circuito.
- Proceso de soldadura: Los procesos de soldadura manual son mucho más fáciles de manejar en circuitos panelizados que en individuales. En el caso de usar hornos de convección para el proceso de soldadura, el ahorro de tiempo y energía es muy importante si procesamos al tiempo un panel en lugar de un circuito a la vez.
- Proceso de inspección: Si el proceso de inspección en búsqueda de errores es visual, resulta más fácil revisar la misma sección de componentes en todos los circuitos que contiene el panel que revisar todos los componentes y soldaduras en una sola tarjeta. Los procesos automáticos de inspección por análisis de imágenes (AOI) en búsqueda de defectos, son dramáticamente mas rápidos al procesar un panel, señalando al operador los defectos para ser corregidos y obteniendo además de producto final sin defectos, el registro y la ubicación de los errores en las tarjetas que deberán ser reparadas posteriormente.
Características que debe tener un panel de circuitos impresos:
- Pestañas de soporte: Se requieren mínimo dos pestañas paralelas a lo largo del panel para ser soportado en los diferentes rieles de sujeción y transporte en los procesos de ensamble. La medida requerida usualmente es 1.5 cm.
- Fiduciales de panel y perforaciones de soporte: Esta es una ayuda para el fabricante y se deben ubicar, sobre las pestañas de soporte y cercanos a sus esquinas. Las perforaciones de cada pestaña deberán estar a igual distancia del borde de corte y servirán para la fijación mecánica del panel. Los fiduciales son usados para el posicionamiento automático de las máquinas que intervienen en los procesos de ensamble. Debemos consultar al fabricante cuáles son sus requerimientos al respecto.
- Fiduciales de tarjeta: Se requieren para lograr precisión en los procesos de colocación de componentes SMD e inspección de defectos AOI.
En el siguiente enlace, se describen los detalles de diseño de fiduciales y se incluyen las correspondientes librerías para los programas de diseño electrónico más comunes.
Que son fiduciales y como diseñarlos
- Distancia de los componentes a los bordes: Todos los circuitos deberán tener los componentes alejados de los bordes de corte, una distancia suficiente para que la herramienta que separará nuestras tarjetas una vez termine su proceso de ensamble, no los afecte.
- Tamaño del Panel: Si el proceso de ensamble va a ser implementado por nosotros mismos, el tamaño lo determinara el procedimiento utilizado para soldar ya sea manual o por la capacidad del horno de convección. Si enviamos a un fabricante nuestro panel para ser ensamblado en procesos automáticos, debemos preguntar por el tamaño requerido para obtener la mayor eficiencia en el proceso.
- Proceso de separación de circuitos ya ensamblados: El panel deberá tener la fortaleza y estabilidad suficientes durante el proceso de ensamble, para no doblarse ni romperse por las líneas de corte diseñadas por el usuario. Adicionalmente, su diseño deberá permitir la separación fácil de las tarjetas una vez ensambladas sin deteriorar los componentes, ni los bordes de nuestras tarjetas.
- Líneas de corte: Para evitar confusiones deberemos marcar todas las líneas por donde va a pasar la herramienta que se utilizará para trazar las líneas de corte de nuestros circuitos, incluyendo la correspondiente a las pestañas de sujeción implementadas en el panel.
- Componentes que sobresalen de la tarjeta: Las tarjetas que contengan componentes cuyo borde coincida exactamente o que sobresalgan de los bordes del circuito, deberán panelizarse dejando el espacio suficiente entre ellas para que una vez el componente sea montado no interfiera con la herramienta de separación de las tarjetas arriesgando su integridad, ni con los componentes de la tarjeta vecina.
La figura siguiente muestra un panel diseñado con la separación correcta entre tarjetas para permitir que los conectores Molex que sobresalen del borde derecho de nuestra tarjeta, sean ensamblados y soldados al mismo tiempo que todos los demás componentes.
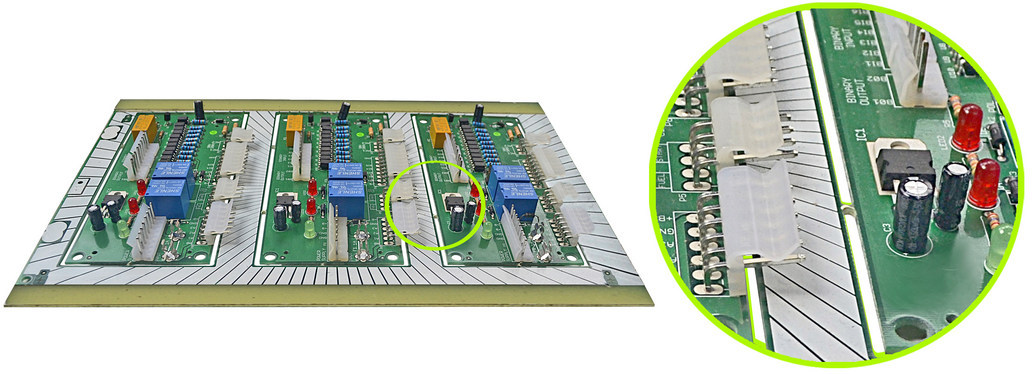
De no tomarse esta precaución, dicho componente no podría ser ensamblado durante el proceso automático y su soldadura deberá efectuarse manualmente disminuyendo la optimización del proceso y aumentando los costos.
- Tipo de corte: En el caso de ordenar a un proveedor solo los circuitos panelizados, deberemos elegir qué tipo de corte queremos manejar de acuerdo a los requerimientos de nuestra tarjeta o del proveedor del servicio de ensamble. Existen básicamente dos tipos de corte que tienen características diferentes de diseño y métodos de separación de las tarjetas que deberemos evaluar por separado:
Corte tipo V-Scoring:
V-Scoring es el término usado para definir los cortes rectos en forma de “V” hechos por el fabricante a lo largo y ancho de un panel, con ángulos de 30 o 45 grados, ubicados simétricamente opuestos en sus dos caras y con una profundidad por lado usualmente de 1/3 del espesor total del panel.
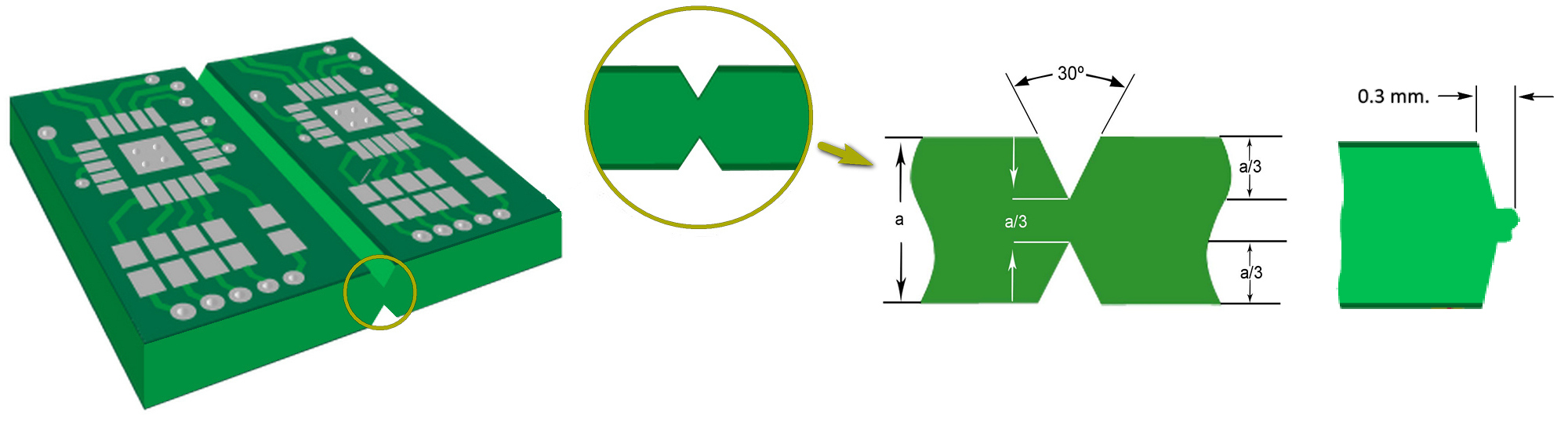
Tamaño final: El usuario deberá tener en cuenta que este tipo de corte aumenta el tamaño del circuito hasta en 0,3 mm. más, debido al ángulo que tiene la herramienta que se utiliza para efectuar el proceso.
Procedimiento de panelizado para corte tipo V-Scoring:
- Después de haber dibujado en la capa adecuada (usualmente, Border Edge, Mechanical 1, etc.) la línea de corte para nuestra tarjeta, seleccionamos en un grupo todas las capas de nuestro circuito y las copiamos tantas veces como sea necesario una al lado de la otra, manteniendo una distancia entre sus bordes de 0.6 mm.
El siguiente enlace ilustra el procedimiento sugerido y las precauciones que se deben tener en cuenta para trazar la línea de corte en circuitos impresos.
Como diseñar la línea de corte en circuitos impresos
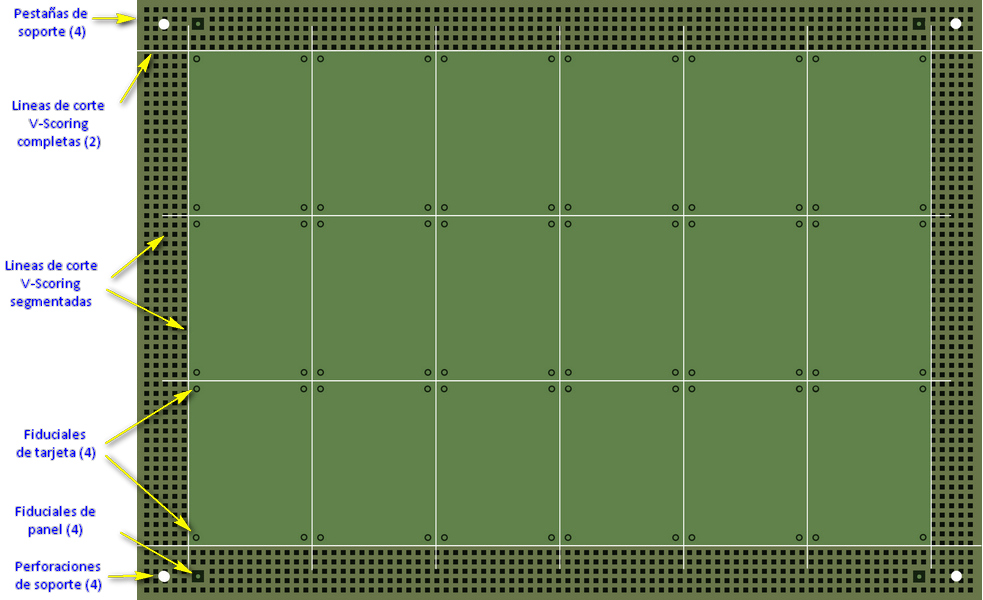
- En una capa diferente trazamos las líneas por donde el fabricante pasará la herramienta para producir el corte tipo “V”. Estas líneas deberán ser de 0.2 mm. y deberán pasar por la mitad de la distancia entre las líneas de contorno de los circuitos de nuestro panel que hemos diseñado hasta el momento. Su recorrido deberá ser de un extremo a otro en los lados más largos del panel como se ilustra en la figura superior e idealmente deberán ir de un borde interno al otro de las pestañas de soporte del panel para mantener su fortaleza durante los procesos de ensamble evitando que se doble por las líneas de corte.
- Debemos comunicar al fabricante que el corte que requerimos es del tipo V-Scoring. La siguiente figura ilustra el procedimiento descrito implementado en un programa de diseño:
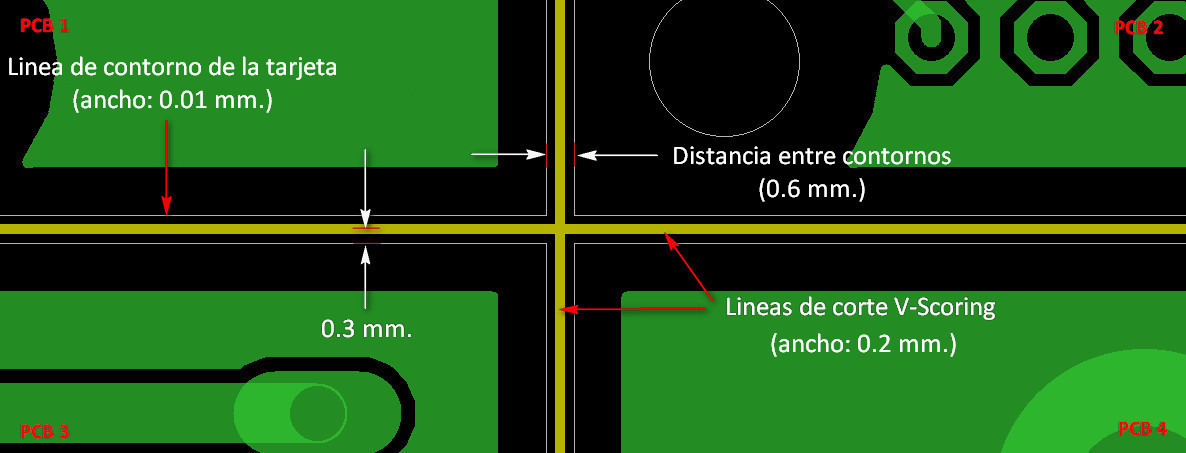
Procesos de separación de las tarjetas panelizadas con tipo de corte V-Scoring
- Manual. Este procedimiento puede ser implementado manualmente doblando el panel por su lado más largo hasta quebrarlo y luego separando las tarjetas haciendo el mismo procedimiento por su lado más corto. Debido al rompimiento de las fibras del sustrato, es necesario suavizar el borde final de nuestra tarjeta mediante un proceso de pulido o lijado.
Otro método manual es hacer pasar un bisturí o una cuchilla circular como las utilizadas para cortar pizza, a través de los canales V-Scoring hasta lograr separar los circuitos. El borde final obtenido es un poco más suave que el anterior pero igualmente debe ser suavizado.
Precaución: Cualquier procedimiento de pulido que involucre fricción de la tarjeta deberá ejecutarse tomando estrictas medidas de protección ESD ya que el proceso generará electricidad estática que afectará indudablemente los componentes ensamblados.
Este procedimiento se efectúa utilizando una máquina depanelizadora donde la tarjeta pasa por dos cuchillas de corte ubicadas una circular en la parte superior y otra recta en la parte inferior del V-Scoring lo cual produce un borde limpio, no tan ideal pero uniforme y aceptable para la mayoría de productos electrónicos. Las figuras adjuntas ilustran el tipo de borde producido por los dos procedimientos.
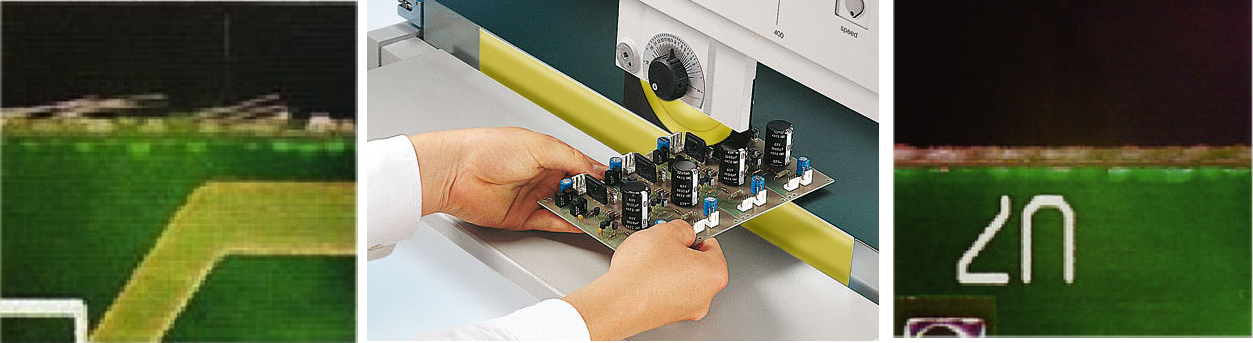
Distancias de borde requeridas para pistas y los componentes:
La siguiente tabla ilustra un poco el proceso de separación de las tarjetas y muestra los valores sugeridos para las distancias del borde en función de la altura de los componentes ubicados cerca de las líneas de un corte tipo V-Scoring:
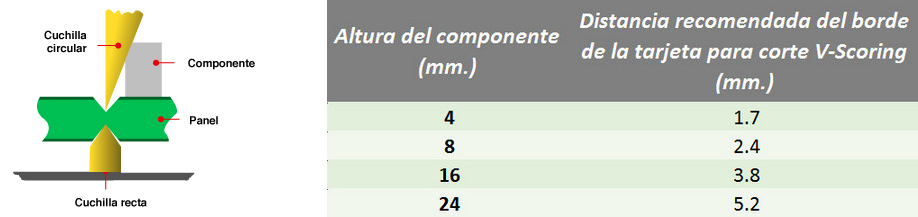
Restricciones: Debemos evitar colocar componentes SMD especialmente condensadores cercanos a los bordes de corte tipo V-Scoring ya que son muy susceptibles a micro fracturas cuando doblemos el panel o cuando el disco pase cerca de ellos cortando el espesor de lámina restante para separar los circuitos ya ensamblados. En el caso de que fuera estrictamente necesario conservar la ubicación de dicho componente este deberá colocarse con su lado más largo paralelo a la línea de corte para transmitir el menor “Stress” al componente al momento de efectuar el proceso tal como se ilustra a continuación:
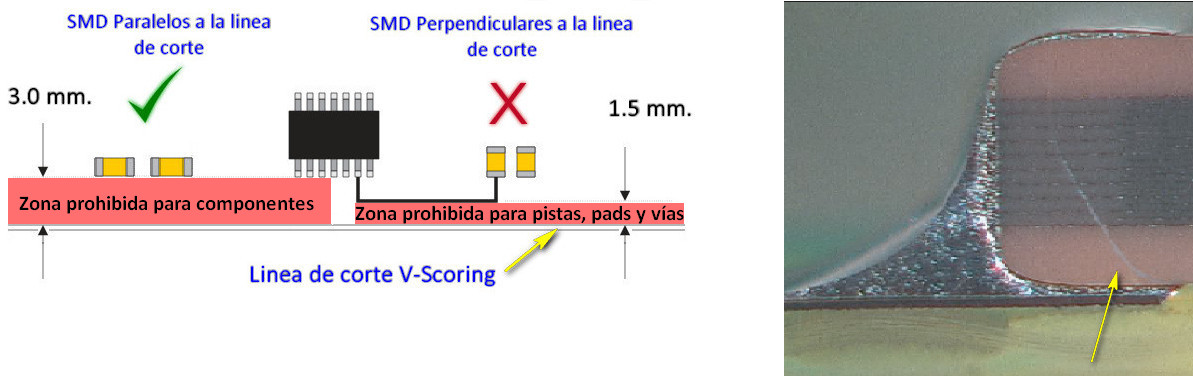
Corte tipo Tab-Routing:
Tab-Routing es el término usado para definir los cortes hechos por el método de ruteo utilizando una fresa de un diámetro usualmente entre 1 mm. y 2.4 mm., que va cortando las tarjetas en el panel, desplazándose por el centro de la línea de corte marcada, y siguiendo su contorno dejando a su paso espacios de lámina perforados (Tabs), de un ancho entre 3 y 5 mm. para dar estabilidad y fortaleza al panel donde el usuario lo requiera para efectuar un exitoso proceso de ensamble.
Forma y tamaño final: Este tipo de corte ademas de ser muy preciso, su calidad de borde es excelente, eliminando la necesidad de efectuar procesos adicionales de pulido. Es utilizado para obtener formas irregulares de tarjetas que necesitan precisión al momento de ser ensambladas en cajas con medidas y formas específicas.

Procedimiento de panelizado para corte tipo Tab-Routing:
- Después de haber dibujado en la capa adecuada (usualmente, Border Edge, Mechanical 1, etc.) la línea de corte para nuestra tarjeta, copiamos todas las capas de nuestro circuito tantas veces como sea necesario una al lado de la otra, manteniendo una distancia entre ellas igual al diámetro de la herramienta usada por el fabricante para tal fin. (Usualmente esta medida es 2.4 mm.)
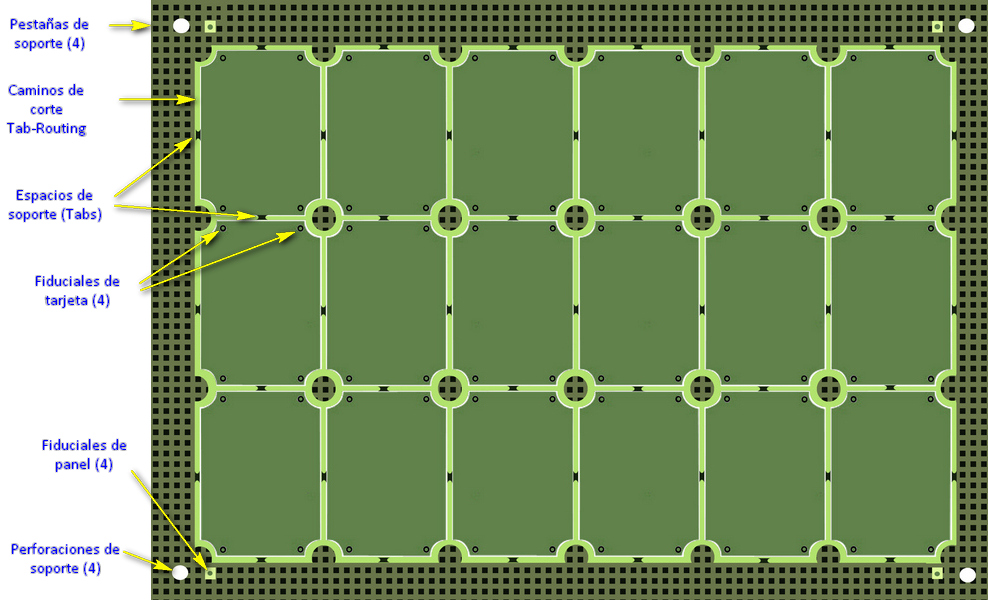
- Posteriormente en otra capa (usualmente Milling, Mechanical 2, etc.), deberemos dibujar las líneas por donde el fabricante pasará la herramienta para producir el corte tipo Tab-Routing. Estas líneas deberán ser trazadas por la mitad de la distancia entre dos circuitos de nuestro panel diseñado hasta el momento, y su recorrido deberá seguir el contorno de nuestras tarjetas dejándolas unidas únicamente a través de los Tabs de soporte.
Debemos comunicar al fabricante que el corte que requerimos es del tipo Tab-Routing. La siguiente figura ilustra el procedimiento descrito:
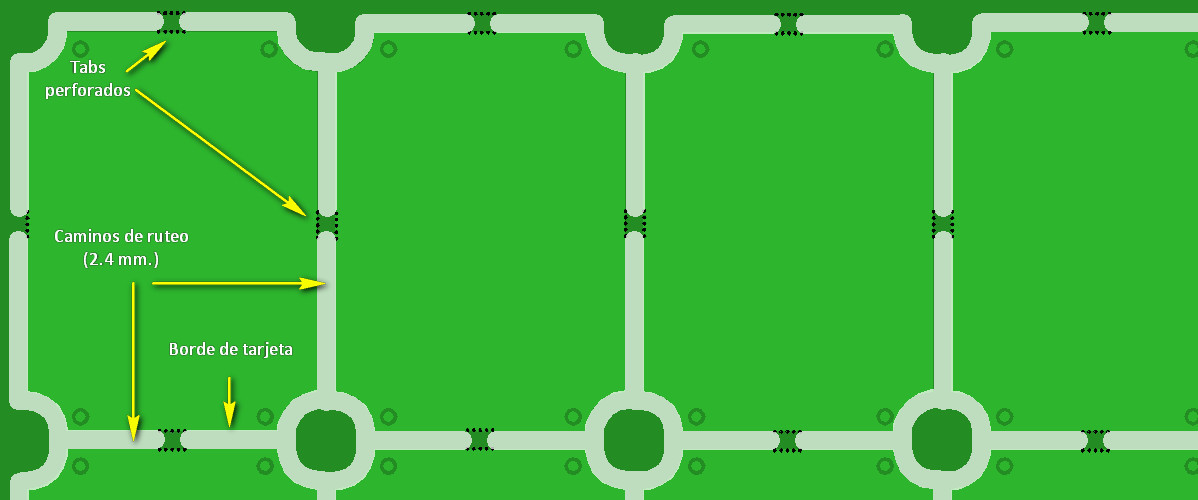
Requerimientos de los Tabs de soporte:
Los Tabs de soporte de las tarjetas pueden elegirse con o sin perforaciones de ayuda al momento de separar los circuitos ensamblados. En el primer caso deberá tener el ancho adecuado que nos permita quebrarlo manualmente manteniendo la rigidez de nuestro panel. Usualmente esta medida varia entre 0.5 mm. y 1.0 mm. de acuerdo al tamaño de las tarjetas y deja un residuo que deberemos pulir para obtener un borde suave.
Para brindar mayor facilidad en el proceso de separación manual de las tarjetas ensambladas, podemos elegir Tabs con perforaciones en uno o ambos lados del corte conservando las características que a continuación se describen:
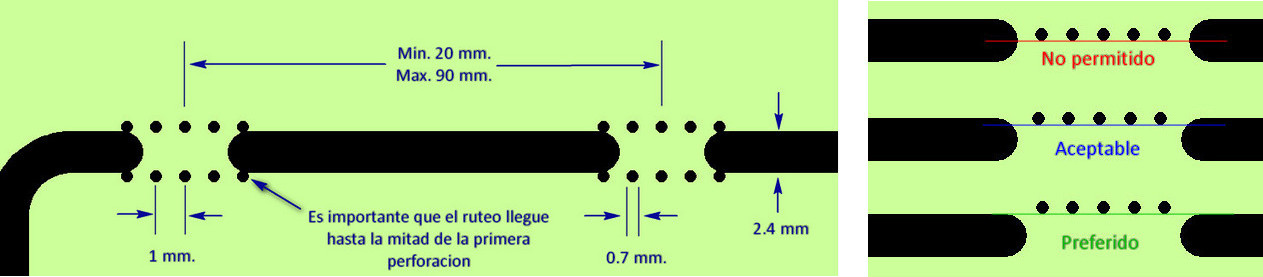
- Diámetro de las perforaciones: 0.7 mm.
- Cantidad de perforaciones: Mínimo 3. Máximo 5.
- Distancia entre perforaciones: 1 mm.
- Ubicación de las perforaciones: La figura superior derecha ilustra la ubicación preferida de las perforaciones para obtener el borde correcto después de separar los circuitos ensamblados.
- Distancia mínima entre Tabs: 20 mm.
- Distancia máxima entre Tabs: Entre 70 y 90 mm.
- Restricciones: De ninguna manera deberán ir ubicados en las esquinas de las tarjetas ni debajo de componentes cuyo cuerpo se extienda hasta el borde o sobresalga mas allá de la tarjeta.
Procesos de separación de las tarjetas panelizadas con tipo de corte Tab-Routing:
Este procedimiento puede ser implementado manualmente quebrando el panel como se observa en la siguiente figura y luego con la ayuda de una pinza se removerán los Tabs remanentes. El borde producido no requiere pulido alguno a menos que sea una exigencia del usuario final de nuestro producto.
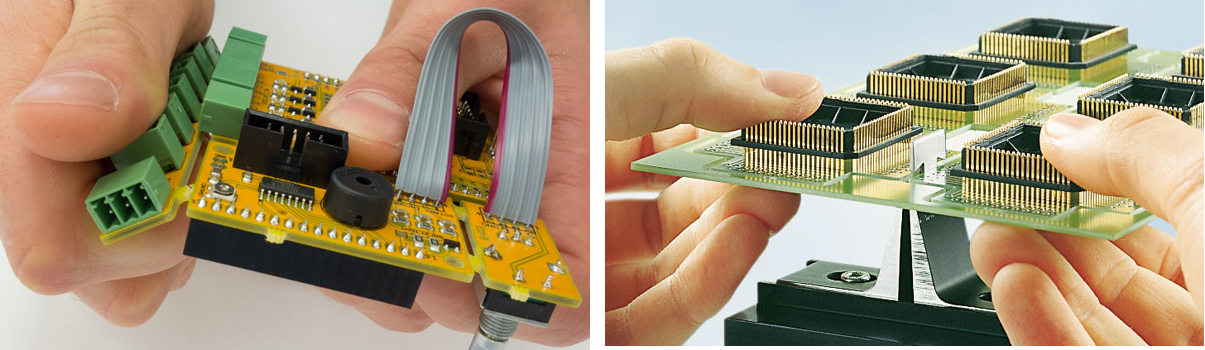
Distancias de borde requeridas para las pistas y los componentes:
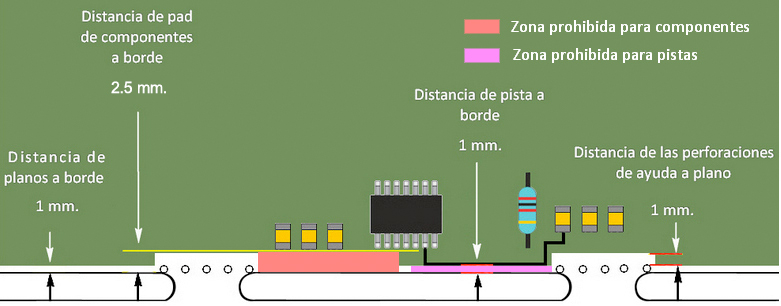
Restricciones: Debemos evitar colocar componentes SMD especialmente condensadores cercanos a los bordes de corte tipo Tab-Routing ya que son muy susceptibles a micro fracturas por efecto del stress transmitido por la flexión del panel cuando quebremos los “Tabs” para separar los circuitos.
Corte tipo mixto V- Scoring y Tab-Routing:
- Se pueden mezclar los dos métodos de panelización para simplificar el proceso o mejorar costos, manteniendo siempre los requerimientos y restricciones para cada tipo de corte.
- Se debe tener en cuenta que habría que pulir los tramos de corte V-Scoring.
- Los dos tipos de líneas de corte deberán ir marcados en capas y preferiblemente en colores diferentes.
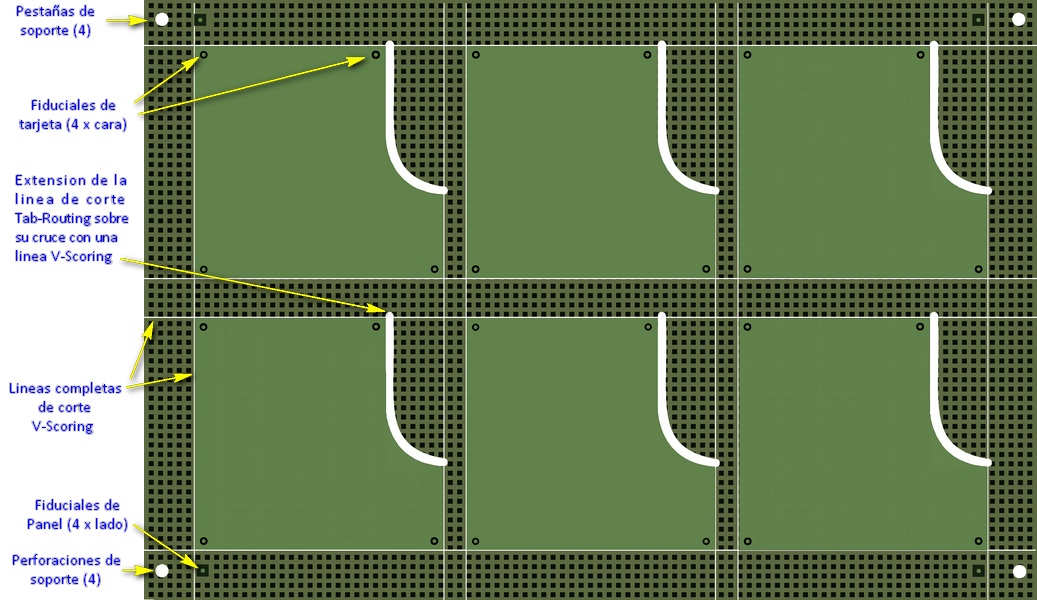
- Los recorridos de las lineas de corte tipo Tab- Routing deberán extenderse mas allá de su encuentro con una linea de tipo V-Scoring cruzando sobre ella una distancia igual a la mitad del diámetro de la herramienta usada. Es decir 1.2 mm. para una herramienta de corte de 2.4 mm.
Panelizado de circuitos circulares:
La rigidez del panel al momento del ensamble de circuitos de forma circular depende de la distancia entre las tarjetas y de los Tabs que la conectan al panel. De ninguna manera es recomendable agruparlos compartiendo la misma linea de corte. Es recomendable guardar una distancia mínima de 10 mm. para mantener la fortaleza del panel en los procesos de manejo y transporte durante su ensamble.
La figura izquierda muestra un panel muy débil ocasionado por no tener distancia alguna entre las tarjetas. A la derecha, vemos un diseño con la robustez necesaria.
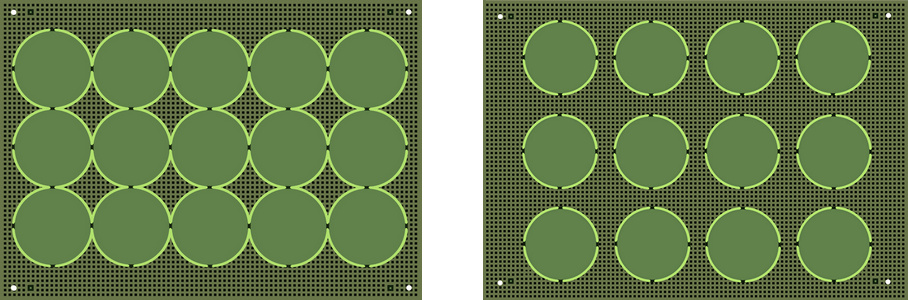
Panelizado de circuitos de referencias y/o formas diferentes:
Además de cumplir las condiciones propias del corte Tab-Routing, este tipo de panelizado requiere de una distancia mínima entre tarjetas de 1 cm. o más dependiendo de si alguna de ellas tiene componentes que sobresalgan de sus bordes, caso en el cual deberá tomarse en cuenta cuanto sobresale y adicionarle este valor a la distancia mencionada. La siguiente figura ilustra esta recomendación:
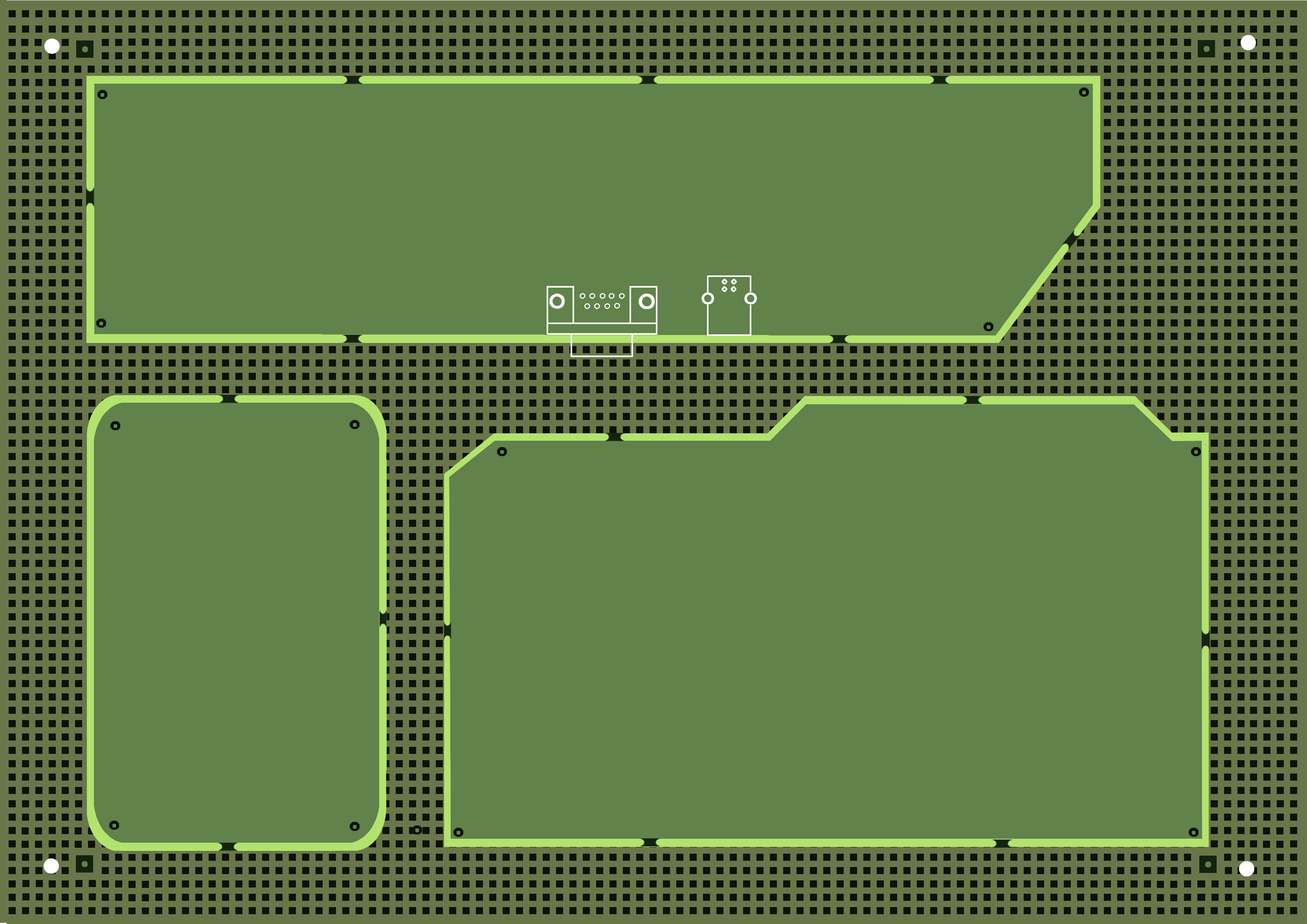
Panelizado de circuitos muy pequeños:
Los circuitos cuyas medidas son muy pequeñas tienden a presentar muchos problemas si se agrupan en panel sin tener la suficiente distancia entre ellos que permita mantener la rigidez requerida para su ensamble. Es recomendable separarlos mínimo 1.5 cm. para obtener esa propiedad y además permitir la entrada de la herramienta de corte del fabricante . En la siguiente figura podemos observar un panel de circuitos muy pequeños agrupados sin la distancia adecuada, ocasionando el doblez del mismo al momento del ensamble por el debilitamiento masivo de la lámina debido a la cantidad de cortes.
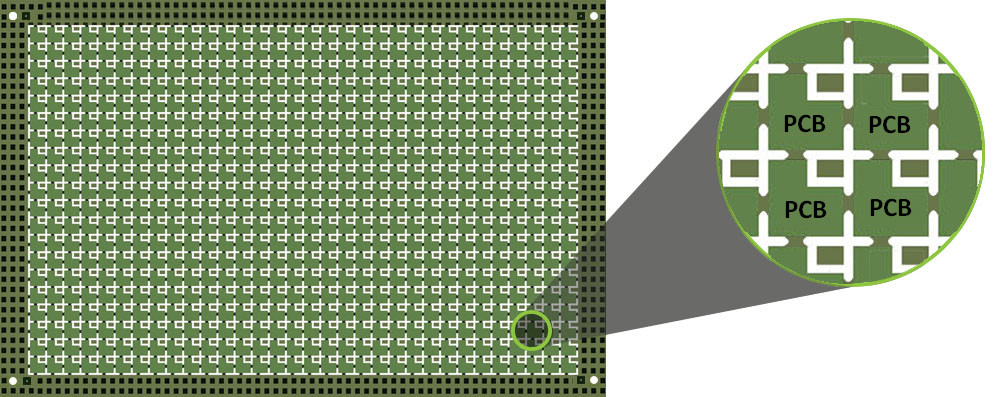
El uso de una correcta separación de las tarjetas permite obtener la rigidez necesaria además de permitir que el proceso de separación sea efectuado sin problema por tener la separación correcta entre Tab como se ilustra a continuación:
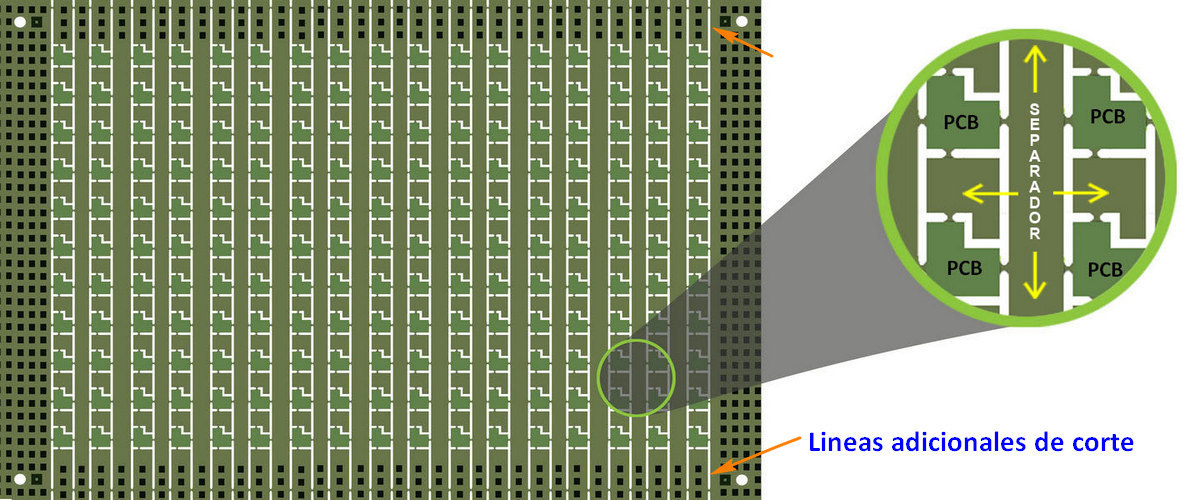
Importante: Si el proceso de separación de las tarjetas ya ensambladas lo efectuamos nosotros y una de sus medidas es menor a 2.0 cm , deberemos trazar los caminos adicionales necesarios para unir filas o columnas, que nos permitan separarlas con facilidad utilizando el método de quiebre manual del Tab, tal como se aprecia en la figura anterior.
PRECAUCIÓN: Las anteriores consideraciones están basadas en las experiencias y prácticas comunes de los procesos de Ensamble de circuitos impresos y son publicadas con propósitos educativos. Úselas bajo su propio riesgo con otros fabricantes.
Buenos días. En la imagen de la sección «Distancias de borde requeridas para las pistas y los componentes». Las dos distancias que están más a la izquierda. Ambas las ponen de 1mm teniendo la misma referencia. Pero en el dibujo no son iguales. Adicional, los colores de la zona prohibidas para componentes y pistas están cruzados entre si.
Saludos.
PD. He estado leyendo todos los artículos y están bastante completos.
¡Hola Luis! Gracias por el comentario, ya corregimos el error y actualizamos el artículo. Saludos.